Did you know the smart factory market is expected to grow significantly over the next few years, with some predicting a compound annual growth rate (CAGR) of 10.3% to 15.47%?
As we move forward in the intelligent systems and AI age, the traditional factory is facing many challenges. These outdated processes can bring downtimes, inefficiency, safety risks, and high operating costs.
For businesses to keep competing, they have to adapt to a transition toward a “smart factory,” but what is this “smart factory,” and how does this help counter these challenges?
A smart factory generally refers to an environment of manufacturing wherein people, machines, and data become connected through advanced technology, thus increasing efficiency and productivity.
It integrates several Industry 4.0 technologies into a flexible, self-optimizing system. These technologies involve cloud software and the Internet of Things (IoT). By incorporating these tools, a smart factory moves beyond conventional automation to create a connected, adaptive system.
Download our free whitepaper on Revolutionizing FMCG: The Industry 4.0 Transformation
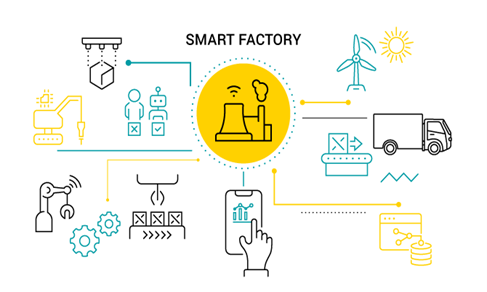
Table of Contents
Why Smart Factories?
Despite advancements in equipment and software, manufacturing productivity has stagnated. From 2007 to 2018, labor productivity grew by only 0.7% per year, far lower than the 3.6% average annual growth between 1987 and 2006.
That would mean productive hours don’t equalize with people’s hours worked. Smart factories have become possible, increasing productivity using automation, data insights, and near-instant optimization, and getting things done with fewer employees at work.
In short, it is falling behind the increase in people’s hours worked rather than advancing as it has for much of the last seventy years.
This brings us to one of the promises of the Fourth Industrial Revolution-to accelerate improvements in operations by connecting machines, people, data, and value chains.
Smart factories deal with these problems through advanced technologies that streamline processes and make them productive.
Let’s look at the benefits of a smart factory:
Greater Productivity and Efficiency
A smart factory integrates the machines, people, and data with the opportunity to analyze the situation and change it at that instant.
Predictability and Decision Making
IoT and AI-driven analytics predict when maintenance will be required and thereby help minimize the costs in terms of lost time through unforeseen failures.
Flexibility and customization
Automated systems and adaptable technology can make smart factories responsive to changing market demands and allow for easier customization and scalability.
Improved Safety and Compliance
It helps identify risk and, through its advanced sensors and monitoring tools, makes the workplace safer with added assurance of compliance with regulations.
Cost Savings
The smart factory reduces waste and saves energy, as automation and optimized resource use mean considerable cost savings over time.
Steps to Build A Smart Factory
Let us look at the step-by-step process of building a smart factory.
1. Assesses Current Capabilities
- Evaluate Infrastructure: Look at the machinery and digital devices currently available.
- Gaps Determination: Look for loopholes in data gathering, automated processes, and connectivity processes.
- Check Readiness: Find how your organization is ready for smart technologies.
2. Define Clear Goals
Set Well-defined Objectives: Quantify and make it SMART, like:
- Improve performance
- Minimize breakdown periods
- Improve quality
- Predictive maintenance
Align With Strategy: This Should align with a larger overall business strategy or serve the requirements of a specific customer.
3. Create a Digital Roadmap
- Step-by-Step Implementation: Implement a strategy on how intelligent technologies shall be implemented.
- Identify Key Technologies: Identify the IoT devices, machine learning applications, and data analytics tools that are most appropriate for your factory.
4. Make Key Investments
- Automate Production: Invest in robots and automated machinery in terms of production.
- Connect Systems: Have systems wherein machines share real-time data to improve decisions.
- Utilize AI: Implement AI and ML predictive maintenance and quality control.
- Data Accessibility: Enable scalable remote access in analytics but against cyber threats.
5. Building Interconnected Systems
- Integration of System: All the devices, sensors, and other machines should be integrated into all-inclusive systems.
- Use MES or ERP: MES or ERP should be used to link production to business operations.
- Ensure Real-Time Data Flow: Real-time data flow will be ensured with seamless communication between machines and central analytics.
6. Refine Data Collection and Analytics
- Install IoT Devices: Install sensors in machines to send real-time data feed.
- Advanced Analytics: Through AI, gain insights, predict possible failures, and optimize a process for minimum downtime.
7. Pilot and Test
- Smart Technologies Implementation: Pilot project on the adoption of smart technologies in one production area.
- Measure Performance: Performance will be monitored and measured based on efficiency and quality using key performance indicators.
- Refine on Results: Tailor change implementation strategies as per pilots’ results prior to generalized deployment.
8. Refine and Deploy
- Scale Successful Models: Extend the smart factory model to other successful production lines.
- Continued Improvement: Data-driven analysis for improving efficiencies, cost-cutting, and quality upgrades.
9. Build Workforce Capacity
- Upskill Employees: Develop employees to work with smart technologies and data analytics.
- Encourage the Learning Culture. It instills the culture of a learning organization with the culture of adaptation to new systems.
10. Continuous Improvement
- Monitoring of Performance: System performance is continuously monitored with regard to areas for improvement.
- Show Flexibility to Market Changes: Have the factory dynamic in the face of market changes.
How do we overcome challenges in Smart Factory Implementation?
There are specific challenges with the shift from traditional to smart factories: high investment costs, obsolete legacy systems, cybersecurity threats, information overload, and gaps in workforce skills. All of these challenges can be effectively handled:
Employee Investment: Prepare your employees to meet those requirements by enrolling them in targeted training sessions. Explore partnerships with higher learning institutions or online training sites like Coursera and LinkedIn Learning.
Legacy System Upgrades: Old systems will be gradually replaced by modern ones that work harmoniously with new technologies. This reduces the amount of disruption and ensures compatibility.
Cybersecurity Enhancement: To safeguard sensitive data and systems, use robust cybersecurity frameworks, such as the NIST Cybersecurity Framework.
Data Analytics Tools: Advanced analytics tools, such as Tableau or Microsoft Power BI, will be used to manage and get the insights from the huge amounts of data generated by smart systems.
Manage Change Effectively: Create a culture of openness to change through open communication and strong leadership. To minimize resistance, make the transition in partnership with your employees.
Conclusion
Smart factories are the future of manufacturing, advanced technology, efficiency, customization, and sustainability. At Gramener, we enable businesses to unlock their full potential through automation, AI, and IoT data-driven operations. We break open new levels of productivity and innovation by addressing such problems as cybersecurity and workforce adaptation. Are you ready to jump into the future of smart factories? Let’s begin building it today!
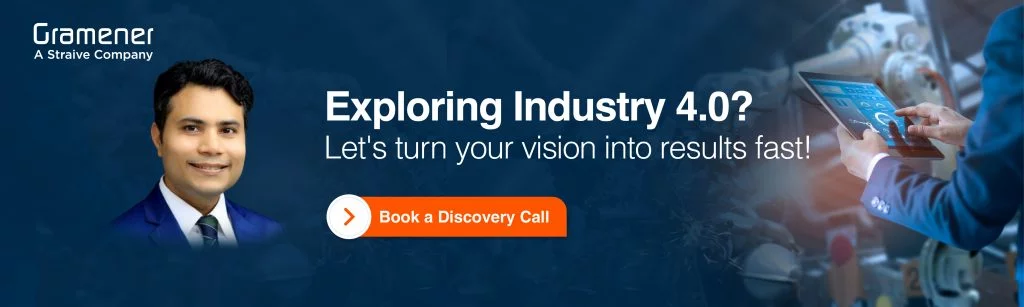